Case StudyRedesigning Research Cage HEPA Filter for Form, Function and Financial Goals
Summary
A longtime manufacturer of life sciences research cages approached R.P. Fedder when the existing design of the filtration system in the cages was no longer profitable or meeting customer needs.
“They were clear that they needed to meet new customer requirements through the design of a filter that was completely retrofittable in their existing cages,” explains Chris Fox, president of R.P. Fedder. “They have hundreds of thousands of cages worldwide, stemming from decades in business.”
By leveraging their experience designing a wide variety of filters coupled with their in-house testing capabilities, R.P. Fedder engineered a simple, elegant, and affordable cylindrical filter design to improve the filtration in the cages. This design was backed with comprehensive statistical data, reassuring the company that the performance of the new filter would meet their needs.
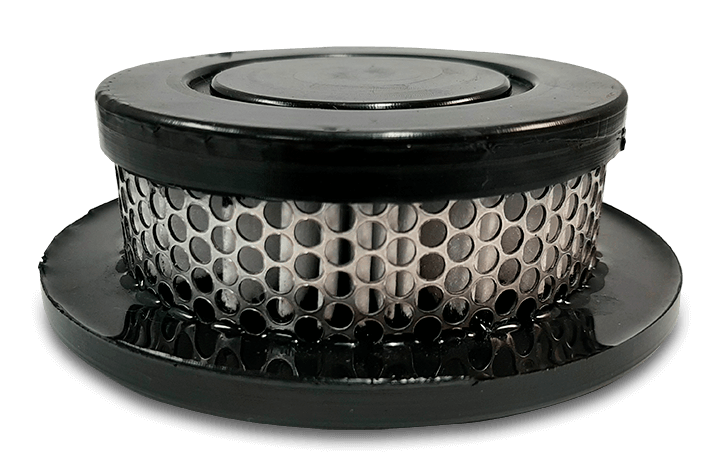
Main Goals for the New Filters
Customer requirements had evolved over the years and the company gave Fedder three main goals for the new filters:
- They needed to be able to go through multiple cycles in an autoclave. The existing filters would only survive a handful of cycles before failure, giving them a short lifespan.
- They had to have exceptionally low resistance to air flow, as it was found that resistance produces noise that stresses the animals.
- Filters had to be true-HEPA, meaning they achieved HEPA performance not just in the filter media, but in the whole assembly.
Additionally, the cage company wasn’t making money on the replacement filters because the design was expensive to produce and market conditions drove the price down. The new filter had to be less costly to produce so it would be profitable.
Design Process & Execution
The existing design had a panel filter wedged into a cylindrical housing—the proverbial square peg in a round hole. Fedder came up with a true cylindrical design for the filter that would fit inside the same geometry as the existing housing.
“We drew from all the filters we’d designed over the years to put together the best model for this unique situation,” says Fox. The company used soft, pliable housing materials to provide tight gasket seals and designed it to fit the round hole, providing more surface area and less pressure drop. They also realized that the glue beads in the existing filter were stressing the filter media (and contributing to failure after autoclaving), so came up with a new glue bead design that would help the filter survive the autoclave cycles. The simple, elegant new design was comprised of four pieces, was easy and inexpensive to make, durable and end-user friendly.
R.P. Fedder conducted theoretical modeling of the pressure drop for prospective designs, as pressure drop was the factor that drove the dimensions of the design. The theoretical modeling allowed them to identify the right design on the first pass, expediting a final solution to the customer.
“Since our customer was particularly sensitive to the pressure drop and HEPA performance, we used our in-house testing abilities to test efficiency and air pressure after the filter ran through several autoclave cycles,” explains Fox. “We came up with robust statistical data that reassured them the filters performed as needed and as they were promising their customers they would.”
R.P. Fedder is now working with the company to develop the next generation of cages, providing expertise to come up with an even more robust, user-friendly, less expensive and longer-life cage design.
Interested in a Custom Filter Design for Your Application?
High-performance custom filters designed & manufactured low-cost from the beginning. Jumpstart your design cycle today.

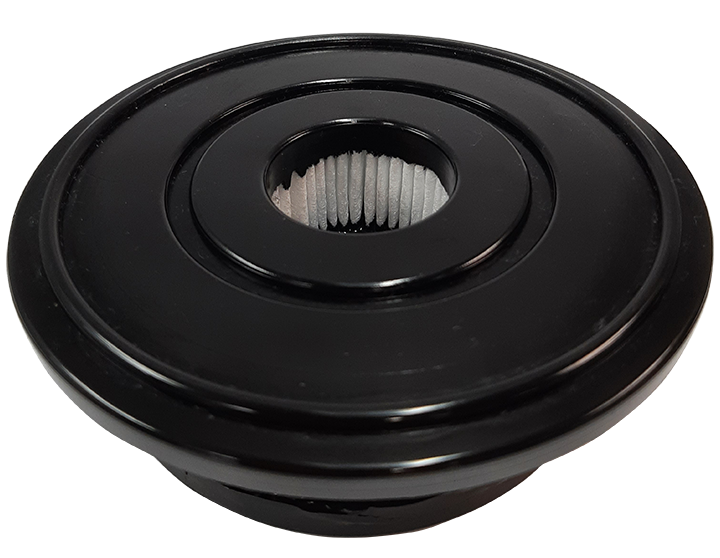