High-Efficiency Cylinder Filters
The Leading Manufacturer of Custom HEPA Filters for 60+ Years
Technology has evolved quite a bit since the very first cylinder filter was developed in the 1970s. Today’s filters are highly efficient, incredibly durable, and yet still very cost-effective.
There are also several different applications in this modern age. From gas turbines to dust collectors and many other industrial settings, you can always rely on R.P. Fedder for high-efficiency cylinder filters in any size, configuration, or media type you need.
Get a Quote
Why Cylinder Filters Are So Effective
Our modern cylindrical filters are designed with your needs and industry regulations in mind:
- Moisture-resistant and humidity-resistant filter media
- Incredibly low drops in pressure at high levels of efficiency
- Anti-rust and anti-corrosion designs possible where end-use requirements call for them
- Reliable stability and structural integrity, even in humid, turbulent, or high-velocity settings
- Maximum dust capacity thanks to optimized pleat depth, filtering area, and number of pleats
- Expressly designed to perform well with low dust concentrations and extremely adhesive dust
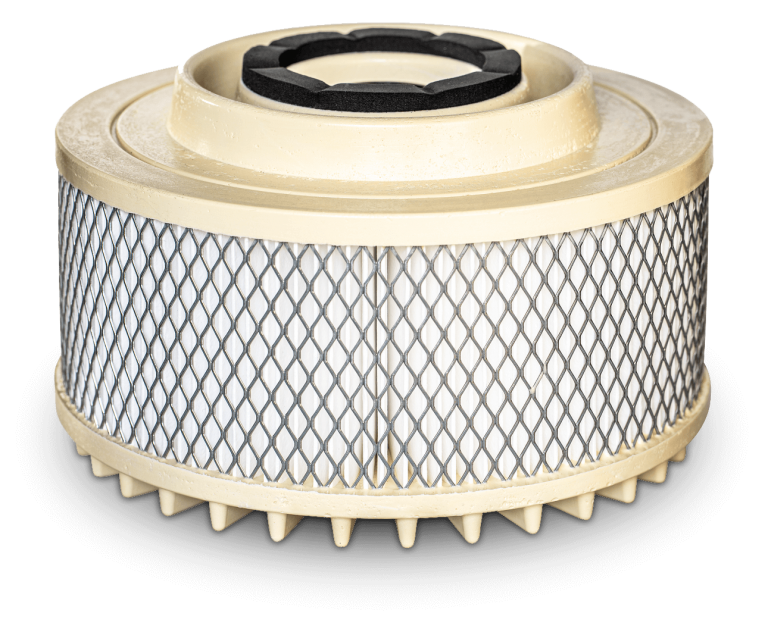
Parts of a Cylinder Filter
Our cylindrical filters are engineered to trap and hold onto fine particles that pollute your airstream. The end result is clean air that complies with workforce health and safety requirements, as well as environmental regulations.
Let’s take a closer look at the technology and mechanics behind our cylinder filters.
Filter Media
Pleats
Inner Cage/Core
End Caps
Seal/Gasket
Mesh or Outer Liner
The filter media does most of the heavy lifting related to trapping particulates. Depending on the setting, it may be made from one of several materials, such as cellulose, synthetic spunbond, or nanofibers. You can even opt for a polytetrafluoroethylene (PTFE) membrane to further improve efficiency.
Usually, the filter media in a cylindrical cartridge is pleated. The pleats increase surface area, which enables even more dust to be collected. The spacing and design of the pleats also impact your filter’s total airflow and efficiency.
This is essentially the “skeleton” that supports the filter media. The inner cage prevents the filter from crumpling or collapsing as air pressure moves through it. In most designs, this section is made of plastic or metal but also perforated to allow maximum airflow.
Both ends of the cylinder filter are sealed with an end cap. These direct air to go through the filter media as opposed to bypassing it. One end normally has some kind of opening or attachment so it fits into the dust collector. The other end can be open or sealed depending on how it’s designed.
You’ll find this soft material on one, or sometimes both, of the end caps. Its purpose is to guarantee an airtight seal during filter installation. This prevents any dust or unfiltered air from circumventing the filter.
Sometimes, a cylinder filter will have a mesh or outer liner to further support the filter media. It also acts as an exterior layer of protection from large or irregular particulates.
Types and Formats of Dust Collector Cylinder Filters
Each dust collector has its own unique design and configuration. That’s why it’s important to ensure the cylinder filter is designed to work perfectly with the specific piece of equipment in question. Here are the most common configurations you’re likely to encounter.
Cartridge Shape
- Classic cylindrical cartridge filters – Thought of as the “standard” design, these filters have a distinct cylindrical shape. The extended length gives your filter even more surface area. These are used in many applications, as well as in many sizes of dust collectors.
- Tapered or cone-shaped filters – This style tapers down to a smaller diameter at one end. You may notice a higher airflow capacity and improved pulse cleaning due to the conical shape.
Oblong or oval filters – Rather than a perfectly circular design, these filters are oblong or oval-shaped. These work well in smaller spaces, as the design can offer more surface area for filtering and a circular filter of the same size.
Cylinder Filter End Cap Formats
- Open/Open design – Both of the filter’s ends are left open so that air can flow freely throughout the entire length.
- Open/Closed design – One end of the filter is open, and the other is closed. This format works well when you need air to flow in a particular way or direction.
Single Open End (SOE) with threaded end – Certain filters are designed with threads on the open end so they may securely screw into the system.
Custom HEPA Filters for Any and All Industries
We proudly support any and all industries that can benefit from working with a custom HEPA filter manufacturer:
- Aerospace
- Air Cleaning
- Air Purification
- Airline
- Animal Caging Systems
- Appliances
- Cabin Air Filters
- CBRN (Chemical, Biological, Radiological, and Nuclear)
- Chemical
- Cleanrooms
- Construction
- Dental Equipment
- Disaster Recovery Ventilation
- Electrical
- Food and Beverage
- Firefighting
- Fume Collection
- General Industry
- HVAC Equipment
- Hybrid Transportation Equipment
- Industrial Vacuum Systems
- Infection Isolation Rooms
- Integrated Circuit Fabrication
- Laser Cutting
- Life Sciences
- Machining and Milling
- Manufacturing Equipment
- Medical
- Military
- MOCVD
- Negative Air Machines
- Off-Road Equipment
- Petrochemical
- Pharmaceutical
- Powered Air Purifying Respirators (PAPRs)
- Precision Machining
- Protective Environment Rooms
- Remediation
- Room Air Purification
- Semiconductors
- Surgical Smoke Filters
- Surgical Suites
- Transportation
- Welding Fumes
Media Types for Industrial Cylinder Filters
There’s a wide range of media types available for dust collector cylindrical filters. To choose the best one for your application, you need to think about the nature of the dust you’re collecting.
Cellulose
Cellulose-polyester blend
Spunbond polyester
PTFE
Nanofiber
Oleophobic
Anti-static
Flame-retardant
Cellulose is extracted from wood pulp. This media is a common fundamental material used in numerous industrial settings. As a nature-derived product, it’s both affordable and effective. However, cellulose can be vulnerable to moisture.
This mix of natural cellulose and synthetic polyester makes for an affordable media that’s also moisture-resistant. Plus, filters with these materials are often more durable and efficient than pure cellulose.
Polyester is extruded into fine filaments, which are then formed into a tight, random mesh and bonded together with heat. This media is popular due to its durability and resistance to chemicals or abrasions. It’s a great choice for high-demand applications. Some of these filters can even be washed and reused several times.
Polytetrafluoroethylene (PTFE) media allows a filter to better trap dust, especially ultra-fine particles, without high pressure drops. The protective layer effectively guards against moisture and many chemicals. This option is another smart choice for arduous conditions.
These filters are designed by interweaving extremely fine fibers over a base media. As a result, they’re highly effective at trapping even submicron dust particles. As a bonus, particles are captured on the filter’s surface, which makes pulse cleaning that much more effective.
In addition to dust, oil-based pollutants are common in industrial facilities. Oleophobic filters repel these particles and keep your airflow consistent. These are indispensable in environments that use a lot of coolants, lubricants, or any other oil-based products.
Certain dust particles can create static electricity, which can be dangerous for your equipment. Ignition is another potential risk. Anti-static media is perfect for these settings. This media is designed to safely dispel static electricity and ensure safety.
A serious step up from anti-static filters, these are engineered for settings where sparks or fire hazards may occur. The flame-retardant chemical treatment ensures that your filter doesn’t become a source of ignition or combustion.
R.P. Fedder: Experts in Commercial HEPA Filters for 60+ Years
Since we were founded in 1959, R.P. Fedder has strived to improve and streamline filtration solutions. Over these 60+ years, our passion for cleaning the air has helped us serve facilities across countless industries.
This dedication extends to every product we offer, including our high-quality replacement commercial HEPA filters. Not exactly sure what you need or don’t see the filter you’re looking for? Contact us for help from one of our specialists.
Understanding MERV Ratings and Cylinder Filters
When it comes to cylindrical cartridge filters, most have a MERV rating in the range of 10 to 16. MERV, short for “Minimum Efficiency Reporting Value,” is a system that measures how effective a filter is at removing pollutants and particles from the air.
A higher MERV rating means the filter is more effective at trapping smaller dust particles. In settings that require a higher rating than MERV 16, you’d typically also install a HEPA after-filter (or an activated carbon option) in addition to your cylinder filter.
Here are the current guidelines regarding MERV ratings for cylinder filters:
- MERV 10 to 13 – As a basic option, these work for large, generally non-toxic particles like atmospheric dust, large mineral dust particles, and sawdust.
- MERV 14 to 16 – With their higher efficiency, filters in this range are best used for smaller or submicron particles, as well as certain fumes (mild steel welding fumes, manufacturing powders, and fine metal dust, for example).
- HEPA after-filter – These are often recommended in settings with hazardous or extremely toxic submicron particles. Collecting nanomaterial, chemical and pharmaceutical manufacturing, and stainless steel welding fumes are common use cases.
- Activated carbon after-filter – When you need filtration on a molecular scale—such as for VOCs, chemical aerosols/vapors, controlling odors, or gas-phase emissions—this type of after-filter can be a wise investment.
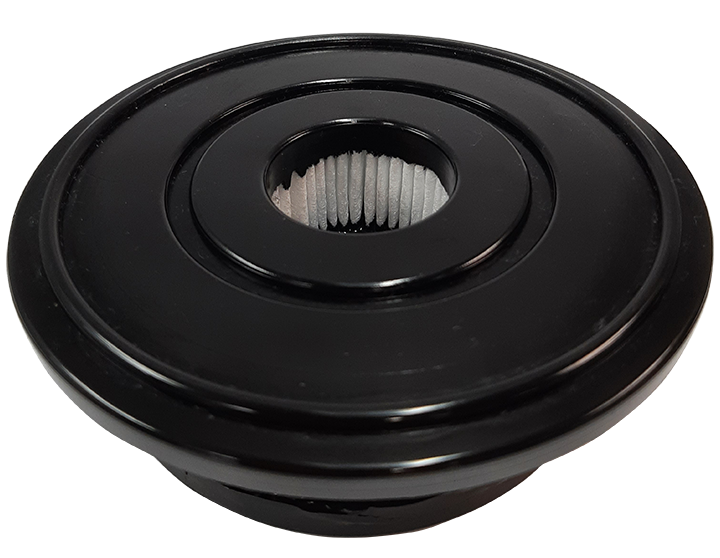
Designing the Ideal Cylinder Filter for Your Specific Needs
Ultimately, there is no one-size-fits-all cylinder filter that’s perfect for every purpose. The ideal solution for your product or end use depends on several factors, like the type of dust you’re dealing with and your IAQ (Indoor Air Quality) requirements.
Here are some of the biggest factors to consider before designing your filter:
- Type of dust – Dust characteristics vary. Whether it’s sticky, abrasive, or chemically reactive, the right filter material needs to be tailored to these properties.
- Size of particles – Dust can range from ultra-fine to highly coarse. Particle size will dictate the type of filter and the level of efficiency required.
- Airflow velocity and volume – Your filter must be robust enough to handle the specific airflow velocity and volume of your system.
- Operating environment – Conditions like humidity, chemical exposure, and temperature can influence the filter’s lifespan and overall performance.
Still have questions about designing the best cylinder filter for your application? Get in touch with our filtration experts here at R.P. Fedder today. With over 60 years of experience in manufacturing, we’ll help you create the perfect solution for your needs.